Plastik parçalar nasıl tasarlanır
Kısa Açıklama:
İçin plastik parçalar tasarlamakparçaların üründe oynadığı role ve plastik için kalıplama işleminin kuralına göre parçaların şeklini, boyutunu ve hassasiyetini tanımlamaktır. Nihai çıktı, kalıp ve plastik parça imalatı için çizimlerdir.
Ürün imalatı tasarımla başlar. Plastik parçaların tasarımı, ürünün iç yapısının, maliyetinin ve işlevinin gerçekleştirilmesini doğrudan belirler ve ayrıca kalıp üretiminin, maliyetinin ve döngüsünün bir sonraki aşamasının yanı sıra enjeksiyonla kalıplama ve işleme sonrası süreç ve maliyeti belirler.
Plastik parçalar, modern toplumda çeşitli ürünlerde, tesislerde ve insanların yaşamlarında yaygın olarak kullanılmaktadır. Plastik parçalar farklı şekil ve işlevler gerektirir. Plastik malzemeler kullanırlar ve özellikleri çeşitlidir. Aynı zamanda, endüstride plastik parça yapmanın birçok yolu vardır. Dolayısıyla plastik parça tasarlamak basit bir iş değil.
Farklı parça tasarımı ve malzemesi farklı işlemlerden üretilir. Plastik kalıplama işlemi esas olarak aşağıdakileri içerir:
1. enjeksiyon kalıplama
2. üfleme kalıplama
3. sıkıştırma kalıplama
4. dönel kalıplama
5. ısıl şekillendirme
6. ekstrüzyon
7. üretim
8. köpüklenme
Bunları toplu olarak üretmenin sayısız yolu vardır. Enjeksiyon kalıplama popüler bir üretim yöntemidir, çünkü enjeksiyonla kalıplanmış% 50 ~% 60 plastik parçalar enjeksiyon kalıplama ile üretilir, yüksek hızlı üretim kabiliyetidir.
Tasarladığımız bazı plastik parçaların durumunu gösterin:
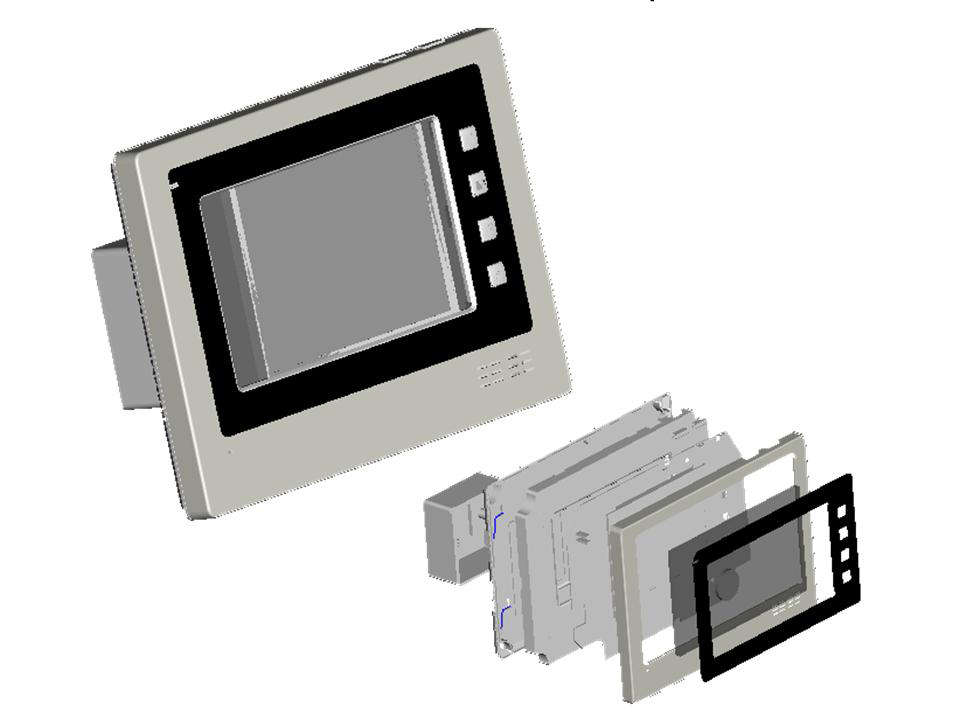
Plastik görüş telefonu muhafazası
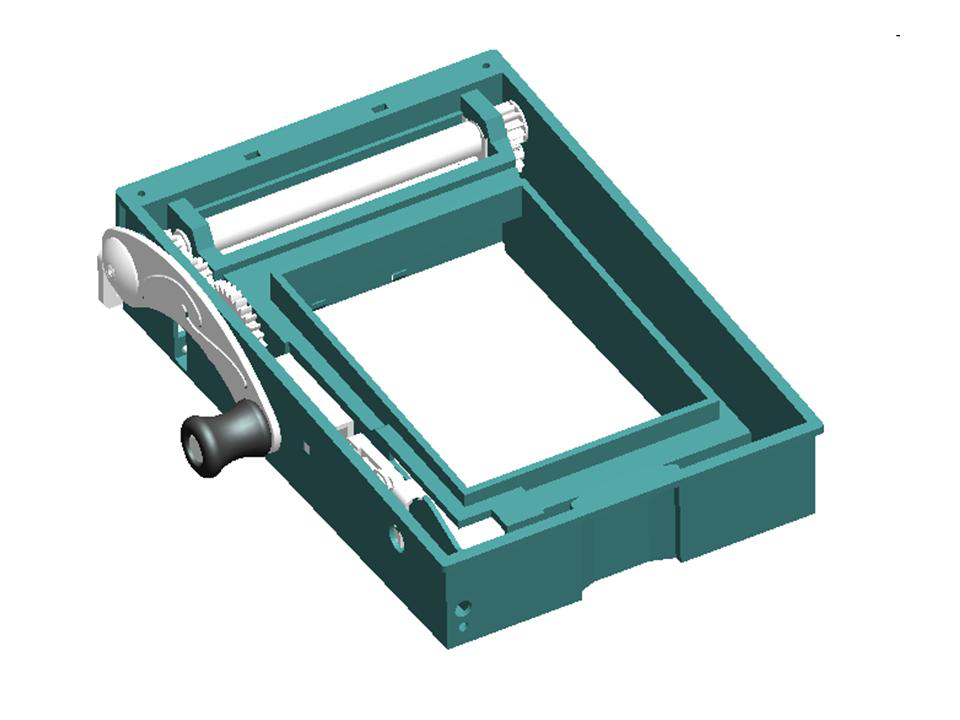
Mekanizmanın plastik parçaları
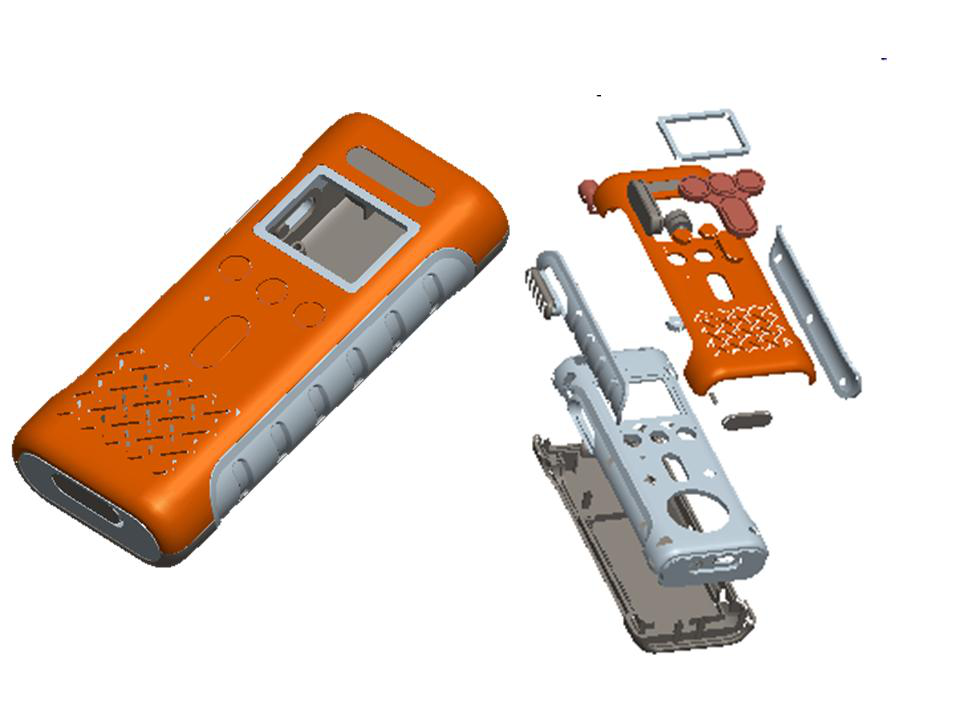
Plastik elektronik kasalar
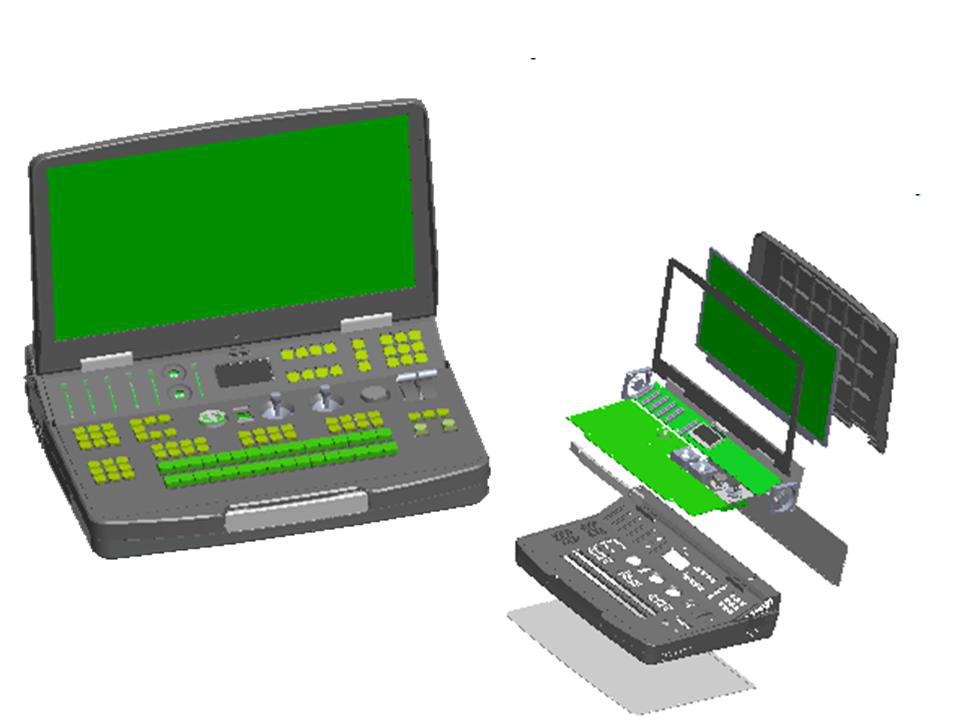
Alet için plastik muhafaza
Aşağıda, plastik parçaların üç açıdan nasıl tasarlanacağına ilişkin ayrıntıları paylaşıyoruz.
* Bilmeniz gereken plastik parçalar tasarlamak için 10 ipucu
1. Ürünün görünüm tasarımını ve boyutunu belirleyin.
Bu, tüm tasarım sürecindeki ilk adımdır. Pazar araştırması ve müşteri gereksinimlerine göre ürünlerin görünümünü ve işlevini belirleyin ve ürün geliştirme görevlerini formüle edin.
Geliştirme görevine göre, geliştirme ekibi ürüne teknik ve teknolojik fizibilite analizi yapar ve ürünün 3 boyutlu görünüm modelini oluşturur. Daha sonra fonksiyon gerçekleştirme ve ürün montajına göre olası parçalar planlanır.
2. Tek tek parçaları ürün çizimlerinden ayırın, plastik parçalar için plastik reçine türünü seçin
Bu adım, önceki adımda elde edilen 3 boyutlu modelden parçaların ayrılması ve ayrı ayrı tasarlanmasıdır. Parçaların fonksiyonel gereksinimlerine göre uygun plastik hammadde veya donanım malzemeleri seçin. Örneğin, ABS genellikle
kabuk, ABS / BC veya PC'nin belirli mekanik özelliklere, abajur, PMMA veya PC lamba direği gibi şeffaf parçalara, dişli veya aşınma parçalarına POM veya Naylona sahip olması gerekir.
Parçaların malzemesi seçildikten sonra detay tasarımına geçilebilir.
3. Çekim açılarını tanımlayın
Çekme açıları plastiğin kalıptan çıkarılmasına izin verir. Çekme açıları olmadan parça, çıkarma sırasındaki sürtünmeden dolayı önemli bir direnç sunacaktır. Parçanın içinde ve dışında draft açıları mevcut olmalıdır. Parça ne kadar derinse, draft açısı o kadar büyük olur. Basit bir kural, inç başına 1 derecelik bir draft açısına sahip olmaktır. Yeterli draft açısına sahip olmamak, parçanın yanları boyunca çiziklere ve / veya büyük ejektör pimi işaretlerine neden olabilir (bu konu hakkında daha sonra daha fazlası)
Dış yüzeyin draft açıları: Parça ne kadar derinse, draft açısı o kadar büyük olur. Basit bir kural, inç başına 1 derecelik bir draft açısına sahip olmaktır. Yeterli draft açısına sahip olmamak, parçanın yanları boyunca çiziklere ve / veya büyük ejektör pimi işaretlerine neden olabilir (bu konu hakkında daha sonra daha fazlası)
Genellikle iyi bir yüzeye sahip olmak için parçaların yüzeyine doku yapılır. Dokulu duvar pürüzlüdür, sürtünme büyüktür ve boşluktan çıkarmak kolay değildir, bu nedenle daha büyük bir çizim açısı gerektirir. Daha kaba doku, daha büyük çekim açısı gerektirir.
4. duvar kalınlığını / düzgün kalınlığı tanımlayın
Enjeksiyon kalıplamada aşağıdaki nedenlerden dolayı katı şekilli kalıplama istenmez:
1) Soğutma süresi et kalınlığının karesiyle orantılıdır. Katı için uzun soğuma süresi, seri üretim ekonomisini bozacaktır. (zayıf ısı iletkeni)
2) Daha kalın bölüm, daha ince bölümden daha fazla büzülür, bu nedenle, çarpılma veya çökme izi vb. İle sonuçlanan farklı büzülme ortaya çıkar (plastiklerin çekme özellikleri ve pvT özellikleri)
Bu nedenle, plastik parça tasarımı için temel kuralımız var; Mümkün olduğunca duvar kalınlığı, parça boyunca tek tip veya sabit olmalıdır. Bu duvar kalınlığına nominal duvar kalınlığı denir.
Parçada herhangi bir dolu bölüm var ise maça sokularak içi boş hale getirilmelidir. Bu, çekirdek etrafında tek tip duvar kalınlığı sağlamalıdır.
3). Duvar kalınlığına karar verirken dikkat edilecek noktalar nelerdir?
İş için yeterince kalın ve sert olmalıdır. Duvar kalınlığı 0,5 ila 5 mm olabilir.
Aynı zamanda daha hızlı soğumaya yetecek kadar ince olmalı, bu da daha düşük parça ağırlığı ve daha yüksek verimlilikle sonuçlanmalıdır.
Duvar kalınlığındaki herhangi bir değişiklik mümkün olduğunca minimum tutulmalıdır.
Değişken duvar kalınlığına sahip bir plastik parça, farklı soğutma hızları ve farklı büzülme yaşayacaktır. Böyle bir durumda yakın tolerans elde etmek çok zor ve çoğu zaman imkansız hale gelir. Duvar kalınlığı varyasyonunun gerekli olduğu durumlarda, ikisi arasındaki geçiş kademeli olmalıdır.
5. Parçalar arası bağlantı tasarımı
Genellikle iki kabuğu birbirine bağlamamız gerekir. Dahili bileşenleri yerleştirmek için aralarında kapalı bir oda oluşturmak için (PCB montajı veya mekanizması).
Genel bağlantı türleri:
1). Kancalar:
Yaylı kancalı bağlantı, küçük ve orta boy ürünlerde yaygın olarak kullanılmaktadır. Karakteristik özelliği, çıtçıtlı kancaların genellikle parçaların kenarına yerleştirilmesi ve ürün boyutunun küçültülebilmesidir. Monte edildiğinde tornavida, ultrasonik kaynak kalıbı ve diğerleri gibi herhangi bir alet kullanılmadan doğrudan kapatılır. Dezavantajı, geçmeli kancaların kalıbı daha karmaşık hale getirebilmesidir. Sürgü mekanizması ve kaldırma mekanizması, geçmeli kanca bağlantısını gerçekleştirmek ve kalıp maliyetini artırmak için gereklidir.
2). Vida bağlantıları:
Vida bağlantıları sağlam ve güvenilirdir. Özellikle, vida + somun sabitlemesi çok güvenilir ve dayanıklıdır, çatlak olmaksızın birden fazla demonte etmeye izin verir. Vidalı bağlantı, büyük kilitleme kuvvetine ve çoklu sökmeye sahip ürünler için uygundur. Dezavantajı, vida kolonunun daha fazla yer kaplamasıdır.
3). Montaj başlıkları:
Montaj başlıkları bağlantısı, çıkıntılar ve delikler arasındaki sıkı koordinasyon ile iki parçayı sabitlemektir. Bu bağlantı şekli, ürünlerin demonte edilmesine izin verecek kadar güçlü değildir. Dezavantajı, sökme süresi arttıkça kilitleme gücünün azalmasıdır.
4). Ultrasonik kaynak:
Ultrasonik kaynak, iki parçanın ultrasonik kalıba yerleştirilmesi ve temas yüzeyinin ultrasonik kaynak makinesinin etkisi altında birleştirilmesidir. Ürün boyutu daha küçük olabilir, enjeksiyon kalıbı nispeten basittir ve bağlantı sağlamdır. Dezavantaj, ultrasonik kalıp ve ultrasonik kaynak makinesinin kullanılmasıdır, ürün boyutu çok büyük olamaz. Söktükten sonra ultrasonik parçalar tekrar kullanılamaz.
6. Kesintiler
Alttan kesmeler, kalıbın iki yarısının da çıkarılmasına engel olan öğelerdir. Alttan kesmeler, tasarımın hemen hemen her yerinde görünebilir. Bunlar, parçadaki bir draft açısı eksikliğinden daha kötü olmasa da, kabul edilemezler. Bununla birlikte, bazı alt kesimler gereklidir ve / veya kaçınılmazdır. Bu durumlarda gerekli
Alt kesimler, kalıp içerisinde kayan / hareketli parçalar ile üretilir.
Kalıbı üretirken alt kesimler oluşturmanın daha maliyetli olduğunu ve minimumda tutulması gerektiğini unutmayın.
7. Destek Çubukları / Köşebentler
Plastik parçadaki nervürler, parçanın sertliğini (yük ve parça sapması arasındaki ilişki) iyileştirir ve sertliği artırır. Aynı zamanda kaburga yönünde eriyik akışını hızlandırdıklarından küflenme kabiliyetini de artırır.
Kaburgalar, parçanın görünüşte olmayan yüzeylerinde maksimum gerilim ve sapma yönü boyunca yerleştirilir. Kalıbın doldurulması, çekilmesi ve çıkarılması da nervür yerleştirme kararlarını etkilemelidir.
Dikey duvarla birleşmeyen nervürler aniden bitmemelidir. Nominal duvara kademeli geçiş, stres konsantrasyonu riskini azaltacaktır.
Kaburga - boyutlar
Kaburgaların aşağıdaki boyutları olmalıdır.
Çukur izini önlemek için nervür kalınlığı, nominal duvar kalınlığının 0,5 ila 0,6 katı arasında olmalıdır.
Kaburga yüksekliği, nominal duvar kalınlığının 2,5 ila 3 katı olmalıdır.
Kaburga, çıkarmayı kolaylaştırmak için 0,5 ila 1,5 derece draft açısına sahip olmalıdır.
Kaburga tabanı, 0.25 ila 0.4 kat nominal duvar kalınlığına sahip olmalıdır.
İki nervür arasındaki mesafe, nominal duvar kalınlığının 2 ila 3 katı (veya daha fazla) olmalıdır.
8. Radyal Kenarlar
İki yüzey birleştiğinde bir köşe oluşturur. Köşede et kalınlığı, nominal et kalınlığının 1,4 katına çıkar. Bu, farklı büzülme ve kalıplanmış stres ve daha uzun soğutma süresi ile sonuçlanır. Bu nedenle keskin köşelerde hizmette arıza riski artar.
Bu sorunu çözmek için köşeler yarıçap ile düzeltilmelidir. Yarıçap, hem harici hem de dahili olarak sağlanmalıdır. Çatlağı teşvik ettiği için asla iç keskin köşelere sahip olmayın. Yarıçap, sabit duvar kalınlığı kuralını doğrulayacak şekilde olmalıdır. Köşelerde duvar kalınlığının 0,6 ila 0,75 katı yarıçapın olması tercih edilir. Çatlağı teşvik ettiği için asla iç keskin köşelere sahip olmayın.
9. Vida başı tasarımı
İki yarım kasayı birbirine sabitlemek veya PCBA'yı veya diğer bileşenleri plastik parçalara sabitlemek için daima vidalar kullanırız. Dolayısıyla vida başları, parçalara vidalama ve sabitleme yapılarıdır.
Vida göbeği şekil olarak silindiriktir. Patron, ana parçaya tabandan bağlanabilir veya yan tarafa bağlanabilir. Yandan bağlama kalın plastik kesite neden olabilir, bu da çökme izine neden olabileceği ve soğuma süresini artırabileceği için arzu edilmez. Bu problem, çizimde gösterildiği gibi çıkıntının bir nervür yoluyla yan duvara bağlanmasıyla çözülebilir. Başlık, destek nervürleri sağlanarak sert hale getirilebilir.
Başlığın üzerinde başka bir parçayı sabitlemek için vida kullanılır. Diş açma tipi vidalar ve diş kesme tipi vidalar vardır. Termoplastiklerde diş açıcı vidalar, elastik olmayan termoset plastik parçalar üzerinde ise diş açma vidaları kullanılmaktadır.
Diş oluşturan vidalar, göbeğin iç duvarında soğuk akışla dişi dişler üretir - plastik, kesilmek yerine yerel olarak deforme olur.
Vida çıkıntısı, vida yerleştirme kuvvetlerine ve hizmet sırasında vida üzerine yerleştirilen yüke dayanacak uygun boyutlarda olmalıdır.
Deliğin vidaya göre boyutu, diş sıyrılmasına ve vidanın dışarı çekilmesine karşı direnç açısından kritiktir.
Başlık dış çapı, diş oluşumundan kaynaklanan çember gerilimlerine dayanacak kadar büyük olmalıdır.
Delik, kısa bir uzunluk için giriş girintisinde biraz daha büyük çapa sahiptir. Bu, içeri girmeden önce vidayı yerleştirmeye yardımcı olur. Ayrıca, çıkıntının açık ucundaki gerilimi azaltır.
Polimer üreticileri, malzemeleri için patronun boyutunu belirlemek için yönergeler verir. Vida üreticileri ayrıca vida için doğru delik boyutu için yönergeler verir.
Baştaki vida deliği etrafında güçlü kaynak bağlantıları sağlamak için özen gösterilmelidir.
Agresif ortamda başarısız olabileceğinden patronda kalıplanmış stresi önlemek için özen gösterilmelidir.
Baştaki delik diş derinliğinden daha derin olmalıdır.
10. yüzey dekorasyonu
Bazen güzel bir görünüm elde etmek için genellikle plastik kasa yüzeyine özel işlem uygularız.
Gibi: doku, yüksek parlaklık, sprey boyama, lazer gravür, sıcak damgalama, elektrokaplama vb. Ürün montajını etkileyen sonraki işlemlerin gerçekleştirilememesi veya boyut değişikliklerinin önlenmesi için ürünün tasarımında önceden dikkate alınması gerekir.