Kalıp sınıflandırması
Kısa Açıklama:
Kalıp (kalıp, kalıp) çok büyük bir ailedir, modern endüstride önemli rol oynar. Endüstriyel üretimi anlamak için açık bir kalıp sınıflandırması çok önemlidir.
Kalıp (kalıp, kalıp) insan faaliyetlerinde kullanılan özel bir araçtır. Kalıp sınıflandırmasıgeniş bir yelpazeyi içerir. Modern toplumda eski, parçaların üretim verimliliğini ve hassasiyetini büyük ölçüde artıran endüstriyel üretimle yakından ilgilidir.
Küf, insan faaliyetlerinde kullanılan özel bir araçtır. Kalıp sınıflandırması geniş bir yelpazeyi içerir. Modern toplumda kalıp, parçaların üretim verimliliğini ve hassasiyetini büyük ölçüde artıran endüstriyel üretimle yakından ilgilidir.
Kalıp, malzemeleri belirli şekil ve boyutlara sahip ürünlere ve parçalara şekillendiren (şekillendiren) teknolojik ekipmandır. Dahil olanlar: damgalama kalıbı, plastik enjeksiyon kalıbı, döküm kalıbı, dövme kalıbı, toz metalurjisi kalıp kalıbı, çekme kalıbı, ekstrüzyon kalıbı, haddeleme kalıbı, cam kalıp, kauçuk kalıp, seramik kalıp, döküm kalıbı ve diğer tipler. Modern endüstride kalıp, esas olarak plastik parçaların ve donanım parçalarının seri üretiminde kullanılan kalıbı ifade eder. Boşluğuna enjekte edilen sıvı plastik, metal ve diğer malzemelerden katı bir cisim oluşturmak için kullanıldığında buna "kalıp" veya "kalıp" diyoruz. Katı boşluğun delinmesi, bükülmesi, bükülmesi ve ekstrüzyonu için kullanıldığında, genellikle buna "kalıp" diyoruz.
Kalıp, özelliklerine göre aşağıdaki şekilde sınıflandırılır:


Malzemelere ve işleme teknolojisine göre sınıflandırma, kalıplar donanım kalıp kalıbı, plastik kalıp ve özel kalıp olarak ayrılabilir.
(1) Metalik olmayan ve toz metalürjik kalıplar: plastik kalıplar, sinterleme kalıpları, kum kalıpları, vakumlu kalıplar ve parafin kalıpları.
Polimer plastiklerin hızla gelişmesiyle birlikte plastik kalıplar insanların yaşamlarıyla yakından ilgilidir. Plastik kalıplar genel olarak şunlara ayrılabilir: enjeksiyon kalıpları, ekstrüzyon kalıpları, gaz destekli kalıplar, vb.
(2) Donanım kalıpları şunlara ayrılır: kalıp döküm kalıbı, damgalama kalıpları (delme kalıpları, bükme kalıpları, çekme kalıpları, döndürme kalıpları, büzülme kalıpları, dalgalı kalıplar, şişkin kalıplar, şekillendirme kalıpları vb.), Dövme kalıpları (böyle kalıp dövme kalıpları, üzme kalıpları vb.), ekstrüzyon kalıpları, kalıp döküm kalıpları, dövme kalıpları vb.
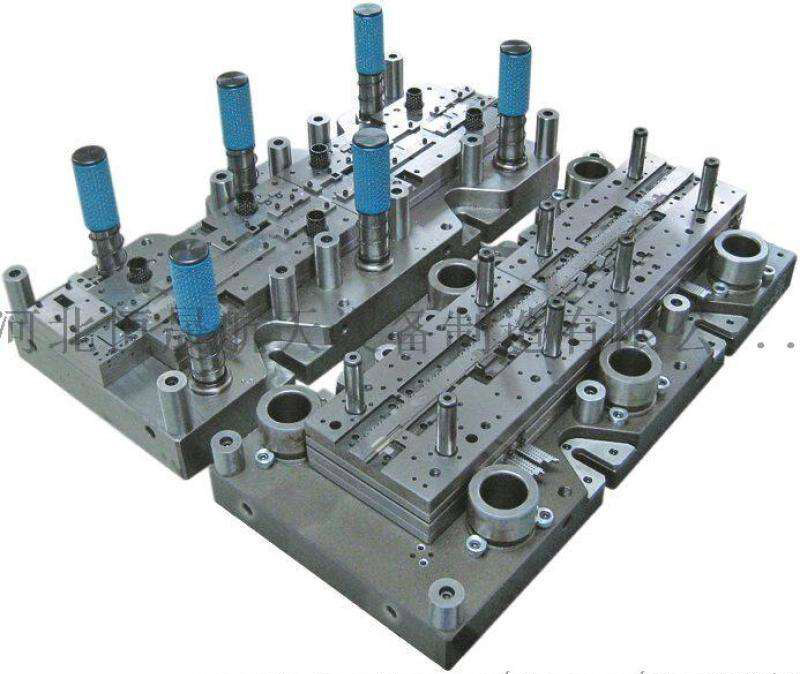
Metal damgalama kalıbı

1. Plastik kalıpların sınıflandırılması
(1) Enjeksiyon Kalıbı
Enjeksiyon kalıbı, termoplastik ve termoset plastiklerin parçalarını oluşturmak için kullanılan bir kalıp türüdür. Enjeksiyon kalıplama, yüksek hassasiyeti ve verimliliği nedeniyle yaygın olarak kullanılmaktadır. Enjeksiyon kalıplama, plastiği enjeksiyon makinesinin ısıtma kovanına eklemektir. Plastik ısıtılır ve eritilir. Enjeksiyon makinesinin vidası veya pistonu ile tahrik edilen plastikler, nozul ve kalıp döküm sistemi ile kalıp boşluğuna enjekte edilir, fiziksel ve kimyasal eylemler nedeniyle enjeksiyon ürünlerinde sertleşir ve şekillenir. Enjeksiyon kalıplama, plastik parçaların enjeksiyon, tutma basıncı (soğutma) ve kalıptan çıkarma işlemlerinden oluşan bir döngüdür, bu nedenle enjeksiyon kalıplama periyodik özelliklere sahiptir.
Termoplastik enjeksiyon kalıplama, kısa kalıplama döngüsü, yüksek üretim verimliliği, kalıpta erimiş malzemelerin küçük aşınması ve karmaşık şekilli, net yüzey deseni ve işaretli büyük plastik parça partileri ve yüksek boyutsal doğruluk avantajlarına sahiptir. Bununla birlikte, büyük duvar kalınlığı değişikliği olan plastik parçalar için, kalıplama hatalarını önlemek zordur. Plastik parçaların anizotropisi de kalite problemlerinden biridir. En aza indirmek için tüm olası önlemler alınmalıdır.
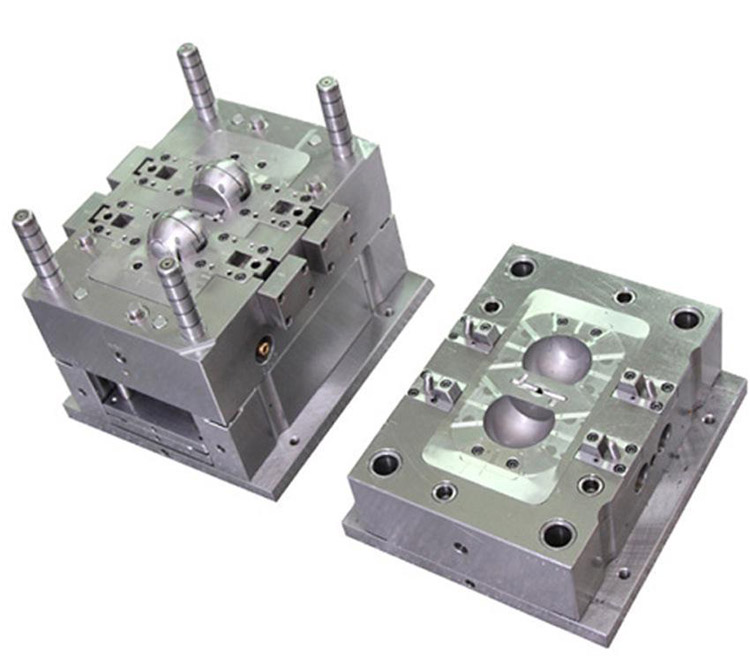
Enjeksiyon kalıbı
(2) Plastik için ekstrüzyon kalıbı
Plastik ekstrüzyon kalıplama, viskoz akış halindeki plastiğin yüksek sıcaklıkta ve belirli basınçta belirli kesit şekli ile kalıptan geçmesi ve daha sonra altta gerekli enine kesit şekli ile sürekli profil haline getirilmesi için bir tür şekillendirme yöntemidir. sıcaklık. Ekstrüzyon kalıplamanın üretim süreci, kalıplama malzemelerinin hazırlanması, ekstrüzyonla kalıplama, soğutma ayarı, çekme ve kesme, ekstrüde ürünlerin son işlemden geçirilmesidir (şartlandırma veya ısıl işlem). Ekstrüzyon işleminde nitelikli ekstrüzyon profili elde etmek için namlu ve ekstrüderin her bir ısıtma bölümünün sıcaklık, vida hızı ve çekme hızının ayarlanmasına dikkat edilmelidir.
Kalıptan eriyen polimerin ekstrüzyon oranının ayarlanmasına özel dikkat gösterilmelidir. Çünkü erimiş malzemenin ekstrüzyon hızı düşük olduğunda, ekstrüdat pürüzsüz bir yüzeye ve tek tip enine kesit şekline sahiptir, ancak erimiş malzemenin ekstrüzyon hızı belirli bir sınıra ulaştığında, ekstrüdat yüzey pürüzlü hale gelecek ve parlaklık kaybedecek ve köpekbalığı derisi, portakal kabuğu, şekil bozulması ve diğer fenomenler ortaya çıkacaktır. Ekstrüzyon hızı daha da arttığında, ekstrüdatın yüzeyi deforme olacak ve hatta dallanacak ve eriyik parçalara veya silindirlere ayrılacaktır. Bu nedenle ekstrüzyon hızının kontrolü çok önemlidir.
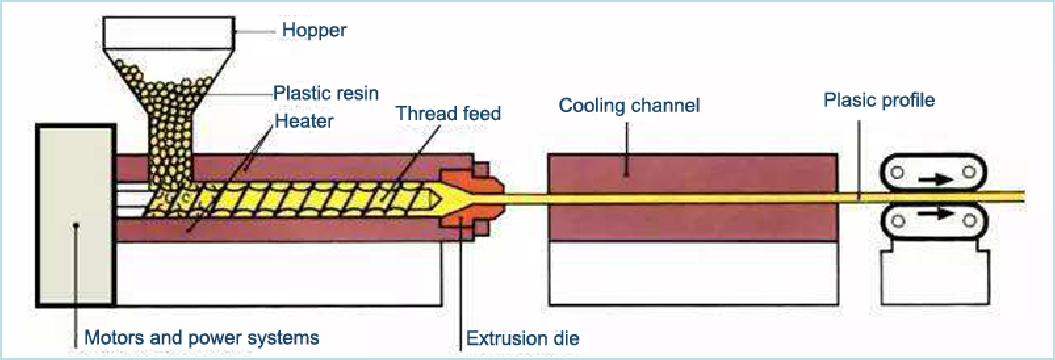
Plastik ekstrüzyon üretim hattı
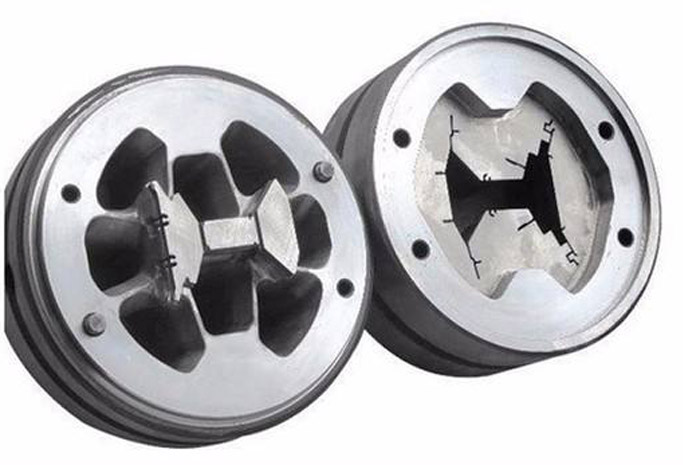
Ekstrüzyon kalıbı
(3) İçi boş kalıp
İçi boş şekillendirme kalıbı, ekstrüzyon üflemeli kalıplama içi boş şekillendirme ve enjeksiyon şişirme içi boş kalıplama içerir.
İçi boş kalıplama, ekstrüzyon veya enjeksiyonla yapılan ve kalıp kalıbında hala plastikleştirme durumunda olan boru veya levha boşluğu sabitleyen, hemen basınçlı hava enjekte eden, boşluğu genişlemeye ve duvarına yapışmaya zorlayan bir tür işleme yöntemidir. Kalıp boşluğu ve soğutma ve sonlandırma işleminden sonra gerekli içi boş ürünleri elde etmek için kalıptan çıkarılır.
İçi boş kalıplama için uygun plastikler, yüksek basınçlı polietilen, düşük basınçlı polietilen, sert polivinil klorür, yumuşak polivinil klorür, polistiren, polipropilen, polikarbonat, vs.'dir. Farklı kalıplama yöntemlerine göre içi boş şekillendirme, ekstrüzyon şişirme kalıplamaya ayrılabilir ve enjeksiyon şişirme. Ekstrüzyon şişirme ile içi boş şekillendirmenin avantajı, ekstrüder ve ekstrüzyon şişirme kalıplarının yapısının basit olmasıdır. Dezavantajı, hamurun çeper kalınlığının tutarsız olmasıdır, bu da kolayca plastik ürünlerin eşit olmayan duvar kalınlığına neden olur. Sağdaki şekil, ekstrüzyon şişirme ile içi boş şekillendirme prensibinin şematik diyagramıdır.
Enjeksiyon şişirme, tek tip duvar kalınlığı avantajına sahiptir ve uçma kenarı yoktur. Enjeksiyon kalıplamanın altından dolayı, içi boş ürünün alt kısmı, sadece güzel değil, aynı zamanda yüksek mukavemet olan birleştirme dikişi üretmeyecektir. Dezavantajı, kullanılan ekipman ve kalıbın pahalı olmasıdır, bu nedenle bu şekillendirme yöntemi çoğunlukla küçük içi boş ürünlerin seri üretiminde kullanılır ve ekstrüzyon üflemeli kalıplama içi boş şekillendirme yönteminin kullanımında yaygın olarak kullanılmaz.
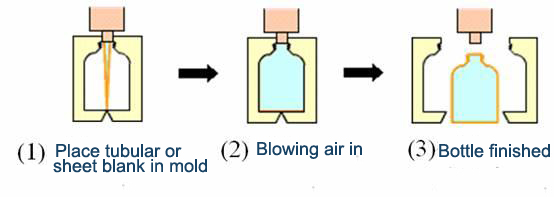
Plastik için enjeksiyon şişirme
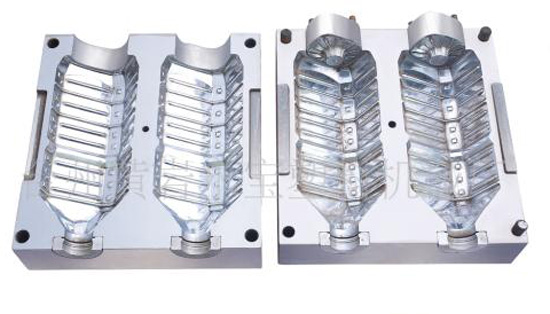
Üfleme kalıpları
(4) Plastik için döküm kalıpları
Basınçlı döküm kalıplarına transfer kalıpları da denir. Plastik malzeme önceden ısıtılmış besleme haznesine eklenir ve ardından basınç sütununa basınç uygulanır. Plastik, yüksek sıcaklık ve basınç altında erir ve kalıbın döküm sistemi vasıtasıyla boşluğa girer, yavaş yavaş sertleşir ve şekillenir. Bu şekillendirme yöntemine basınçlı döküm şekillendirme denir ve kullanılan kalıba basınçlı döküm kalıplama denir. Bu tür bir kalıp çoğunlukla termoset plastik şekillendirme için kullanılır.
(5) Sıkıştırma Kalıbı
Basınçlı kalıplama, plastik parçaların en eski kalıplama yöntemlerinden biridir. Sıkıştırmalı şekillendirme, plastikleri doğrudan açık kalıp boşluğuna belirli bir sıcaklıkta eklemek ve ardından kalıbı kapatmaktır. Isı ve basıncın etkisi altında, plastik bir akış durumuna geçer. Fiziksel ve kimyasal etki nedeniyle, plastikler oda sıcaklığında belirli şekil ve boyutta plastik parçalar halinde sertleştirilir. Sıkıştırma kalıplama esas olarak fenolik kalıplama tozu, üre formaldehit ve melamin formaldehit kalıplama tozu, cam elyaf takviyeli fenolik plastikler, epoksi reçinesi, DAP reçinesi, silikon reçinesi, poliimid vb. Gibi ısıyla sertleşen plastikleri kalıplamak için kullanılır. Ayrıca doymamış polyester agregalarını (DMC), levha kalıplama plastiklerini (SMC), prefabrikasyonu kalıplayabilir ve işleyebilir. Monolitik kalıplama plastikleri (BMC) vb. Genel olarak, sıkıştırma filminin üst ve alt kalıplarının eşleşen yapısı sıklıkla preslenir ve sıkıştırma kalıpları üç türe ayrılır: taşma tipi, taşma olmayan tip ve yarı-taşma tipi.
(6) Basınçlı döküm kalıbı
Kalıp döküm olarak da bilinir. Plastik malzeme önceden ısıtılmış yükleme haznesine eklenir ve ardından kalıbı kilitlemek için presleme kolonu yükleme haznesine yerleştirilir. Basınç, plastiğe presleme kolonundan uygulanır. Plastik, yüksek sıcaklıkta ve yüksek basınçta akıcı bir halde erir ve dökme sistemi ile yavaş yavaş boşluğa katılaşır. Bu şekillendirme yöntemine transfer kalıplama da denir. Basınçlı enjeksiyon kalıplama, farklı erime noktalarına sahip katı plastikler için uygundur. Prensip olarak, sıkıştırmalı kalıplama veya basınçlı enjeksiyon kalıplama için kullanılabilir. Bununla birlikte, katılaşma sıcaklığı katılaşma sıcaklığından düşük olduğunda, erime durumu iyi akışkanlığa sahiptir ve katılaşma sıcaklığı daha yüksek olduğunda katılaşma hızı daha yüksektir.

2. Donanım kalıplarının sınıflandırılması
Ekipman ve proses ortamına göre, metal kalıp sıcak işleme kalıbı ve soğuk işleme kalıbı olarak ayrılabilir. Aralarındaki fark çok büyük.
1) Sıcak çalışma kalıbı: sıcak işleme kalıbı çeliği, sıcak ekstrüzyon kalıbı, kalıp döküm kalıbı, sıcak dövme kalıbı, sıcak şişirme kalıbı vb. Gibi metalin sıcak deformasyonu için uygun kalıbı ifade eder. Sıcak çalışma kalıbı yüksek sıcaklık altında çalıştığı için ve uzun süre yüksek basınç, kalıp malzemesinin yüksek mukavemet, sertlik ve termal stabiliteye, özellikle yüksek termal mukavemete, termal yorgunluğa, tokluğa ve aşınma direncine sahip olması gerekir. Esas olarak şunları içerir:
A. Metal döküm kalıp kalıbı: işlem, gerekli yapısal parçaları elde etmek için yüksek sıcaklıkta erimiş sıvı metali kalıp boşluğuna enjekte etmektir. Metal döküm, alüminyum alaşımı, çinko alaşımı, magnezyum alaşımı ve diğer demir dışı alaşımların karmaşık şekilli parçalarını yapmak için kullanılır.
B. Metal tozu sinterleme kalıbı: işlem, metal tozunu kalıpta belirli bir şekil ve boyutta kütüğün haline getirmek ve daha sonra kütüğü erime durumuna ısıtmaktır, böylece oluşturulabilir. Metal tozu sinterleme esas olarak paslanmaz çelik, titanyum, bakır, demir, nikel ve diğer yüksek sıcaklık alaşımlı parçalar için kullanılır.
C. Metal sıcak ekstrüzyon kalıbı: sıcak işlem sıcak ekstrüzyon kalıbı genellikle alüminyum, magnezyum, çelik ve diğer metallerin yüksek sıcaklık ortamında işlenmesine uygulanabilir ve üretilen parçaların enine kesit şekli değişmeden kalır. Sıcak ekstrüzyon kalıbının iyi ısıya dayanıklı aşınma direncine ve tavlama direncine sahip olması gerekir.

Metal döküm kalıbı
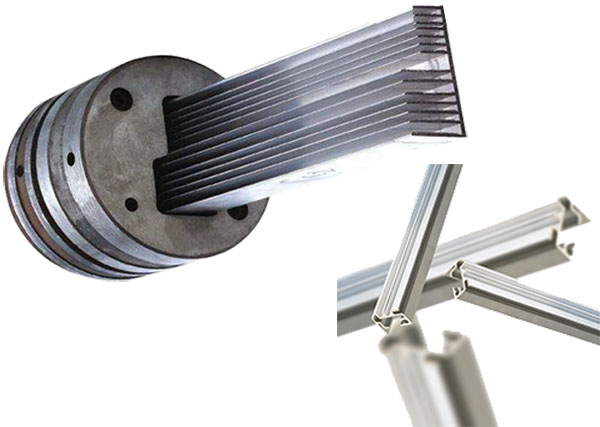
Sıcak ekstrüzyon kalıbı ve alüminyum profil
2) Soğuk işleme kalıpları (Damgalama kalıpları): Soğuk işleme kalıpları çoğunlukla oda sıcaklığında çalışan kalıplardır ve bunlara genellikle damgalama kalıpları adı verilir (delme kalıpları, bükme kalıpları, çekme kalıpları, tornalama kalıpları, büzülme kalıpları, haddeleme kalıpları, şişkin kalıplar gibi) , şekillendirme kalıpları vb.). Soğuk işleme kalıbının çalışan kısmının genellikle çok fazla baskı, eğilme kuvveti, darbe kuvveti ve sürtünme kuvveti taşıması gerekir, bu nedenle deformasyon direnci nispeten büyüktür.
A. Metal kesme kalıbı: metal kesme kalıbı, metal plakadan iki boyutlu şekli kesmek için kullanılır. Parçalar ayrıca bükme, çekme ve şekillendirme için işlenmemiş parça olarak da kullanılabilir. Boşluk, esas olarak çelik, paslanmaz çelik, alüminyum alaşımı, bakır alaşımı ve diğer plakaların kesilmesi, delinmesi ve kırpılması için kullanılır.
B. Bükme kalıbı: plakaları, çubukları ve bölümleri belirli bir açı, eğrilik ve şekle bükmek için bir kalıp kullanan bir parça. Çelik, paslanmaz çelik, alüminyum alaşımlı ve bakır alaşımlı parçalar için uygundur.
C. Çizim kalıbı: Çizim, sac metal malzemeleri silindir veya kutu şekilli parçalara dönüştürmek için damgalama, çekme halkası veya metal kalıp işlemidir. Çizim kalıbı, çizim için yaygın bir araçtır.
D. Şekillendirme kalıbı: Kalıpla şekillendirme kullanarak, kalite ve malzeme özellikleri değişmeden katı üzerinde plastik deformasyonun gerçekleştirildiği bir üretim metodudur. E. Perçinleme kalıbı: metal perçinleme, iki iş parçasını orta iş parçalarına mekanik kuvvetle bağlama yöntemidir. Genellikle düz plakalar arasında perçinleme kullanılır. İşlemde kullanılan kalıba perçinleme kalıbı denir.
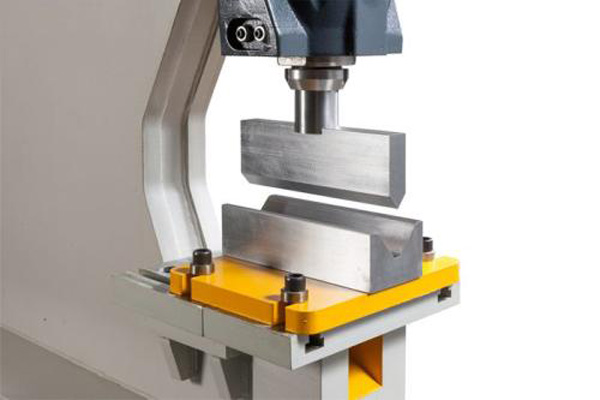
Bükme kalıbı
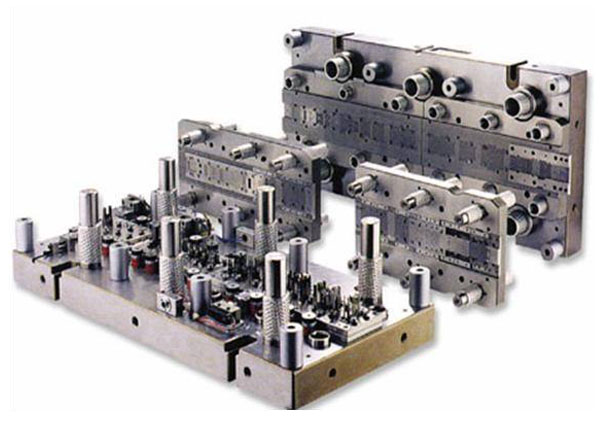
Metal damgalama kalıbı

Kalıpların veya kalıpların uygulanması:
(1). Elektronik ve iletişim ürünleri;
(2). Ofis malzemesi;
(3). Otomobil yedek parçaları;
(4). Ev aletleri;
(5) .Elektrik donanımı;
(6). Tıbbi ve çevre koruma;
(7). Endüstriyel tesisler;
(8). Yapay zeka;
(9). Ulaşım;
(10). İnşaat malzemeleri, mutfak ve tuvalet malzemeleri ve araçları;
